News
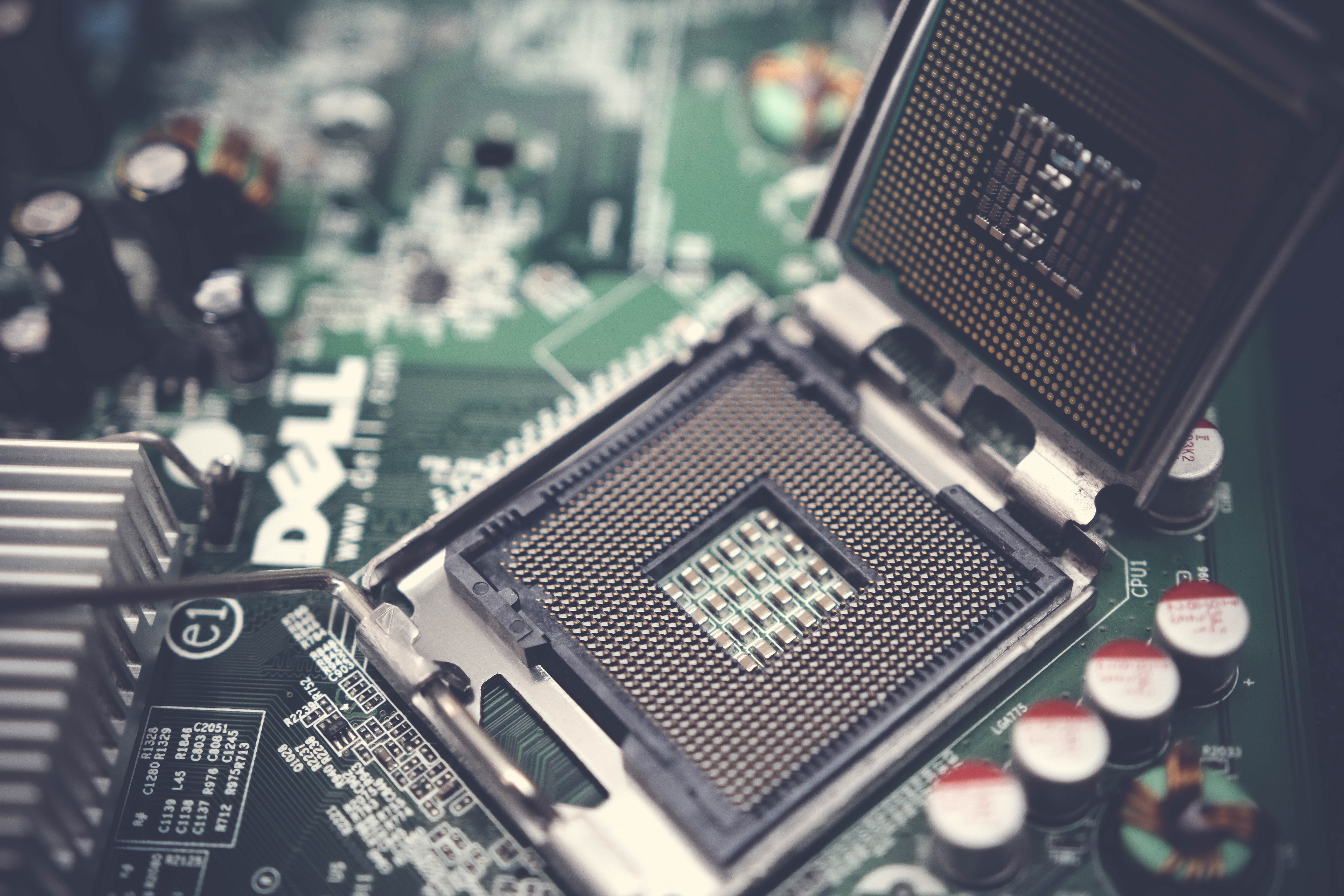
The Black Friday Frenzy - Avoiding Counterfeit Electronics
Black Friday means massive business in electronics, and the circulation of counterfeit components poses problems for manufacturers and consumers alike. Below, we discuss the implications of counterfeit components and how to avoid them.
Whether it’s seeing the news stories of people queuing on freezing cold pavements overnight, or sitting on the internet, enduring long waiting times to enter websites, Black Friday creates a stir in many of us to swoop in on a bargain and save ourselves some cash.
And we’re not alone. A Finder survey discovered that 33% of adults are planning to spend in the Black Friday sales. It’s a notably more conservative figure than recent years, likely caused by budget constraints caused by the pandemic.
Despite belts at home being tightened, the requirements for components in business surges on. Marketing departments across the world compete to outstrip their competitors, selling the ‘must have’ deals and hitting the shelves with new tech releases for Christmas.
‘Tis the season for awareness
The electronics industry is under scrutiny. The global chip crisis continues and the problem of counterfeit components has become an increasing concern for our industry. As a leader in our field, we’ve a duty to care for and protect our clients and the customers that they serve, particularly around this time of year when there is a definite buzz in the air for electronic devices.
So what exactly are the issues with fake components? Counterfeit components pose a significant health and safety risk as they can lead to the failure of the goods in which they are used. These failures, depending on the nature of the goods themselves, can be catastrophic. Perhaps one of the most notable examples of this is the outcomes of using counterfeit components in military equipment.
Even if the fake components work, there is a continued risk in terms of long term reliability. Counterfeit components do not undergo the rigorous testing and quality assurance processes which prevent safety issues in the long term.
The wider implications of counterfeit components
There are also financial risks for manufacturers who fall prey to counterfeit components. If these components are detected after the manufacturing process, they’ll cost considerably more to replace. The maintenance and logistics costs involved if counterfeit components can be significant. A full overview can be found here in the Open Journal of Social Sciences.
Another challenge is detecting the counterfeit components in the first place. The components themselves are usually just a very small part of what makes up the overall end product and they are often introduced much earlier in the supply chain. This means that the components could have been sold by a reputable company, who themselves were unaware of their origins.
The manufacturers of counterfeit components make a great effort to disguise them by duplicating materials, part numbers and serial numbers to make them look authentic. Similarly, counterfeiters have been known to try and pass off lower grade items as higher grade, and therefore more expensive. These issues are compounded by the fact that most manufacturers do not have the resources available to track the origins of every single component that makes up their end product.
Preventative action for your business
So how can your business avoid these counterfeit components and achieve much needed quality assurance? Here at Daletech we appreciate that there always has to be a balance between cost and quality. Our customers are always looking for the cheapest prices on the market so we do our best to provide that by manufacturing competitively, whilst never compromising on quality assurance.
Largely, we achieve this in terms of the staff we have carrying out the manufacturing. We have considerable knowledge and experience across our business, which has been around for over 30 years, giving us and our customers’ confidence that quality standards are continually met and maintained.
Ensuring vital quality assurance
We also strictly follow the ISO 9001:2015 the world’s most recognised quality management system standard. This certification gives our customers assurance that everything we do is traceable, from purchasing components from trusted supply chains; to ensuring that we can trace every part of an assembly at all times when in our manufacturing. All of our assemblies are serial-numbered, which gives each assembly full traceability.
When we receive a new enquiry, we log it on our software, which is used to track all of our jobs. Then once we have a finalised Bill of Materials (BOM), we create an estimate that triggers our software to log every single step of the purchasing process, carefully documenting and monitoring.
In addition, we have live links with our suppliers, which allows us to keep on top of availability in real-time. The end result of this way of working is a product that has incredible traceability and detail surrounding it. We know the origin of our components, the individual staff who have worked upon them and the dates of manufacture. This traceability means that we can fully trust our suppliers; we know who they are and we are confident that they have been fully reviewed.
It is fair to say that our processes are not without their challenges, especially in our current climate of fuel and driver shortages, as well as a lack of skilled workers, not to mention Brexit and the Coronavirus pandemic.
Addressing our industry’s ongoing challenges
We have talked through some of the issues we are facing in the industry at great length in recent months, specifically supply chain management in a post-Brexit world as well as the impacts of the Coronavirus pandemic, both of which have impacted our business significantly. However, we have taken the time to adapt and overcome these challenges.
When sourcing components, we try to use UK based companies where possible, which isn’t easy at a time where supply chains are incredibly complex. Components are no longer made in the UK, so we import through distribution - never directly. This allows us to obtain the confirmation that the source is sending us true components rather than fake components.
The long lead times and driver shortages right now are another obstacle to our business, and we have found that communication is vital. We regularly keep in contact with our customers, often speaking on a daily basis to update them as to where their product is, where in the cycle it is and when we can dispatch it. This transparency ensures that our customers can plan and prepare accordingly.
The skills gap in electronics manufacturing is well documented, as graduates seek out employment in other sectors, traditional manufacturing has suffered. This is challenging for us working in an industry where skilled workers are intrinsic to our overall success. In order to overcome the skills gap, we upskill and nurture our existing workforce and talent pool wherever we can and we are very proud of our growing apprenticeship scheme.
We understand that engineering, design and manufacturing jobs in the electronics sector are highly skilled and multi-faceted, making it even more important (and exciting!) to invest in in-house training. Equally, we’re mindful that we have a role to play in the work experience of our future generation of engineers.
Ultimately, despite the challenges our industry is facing, we work with our customers and problem solve alongside them, as a true partnership. We understand that if our customers aren’t successful, then we won’t be either.
A business to trust
So as the hype around Black Friday looms, the problems posed by counterfeit components may have really come into focus for your business, whether you have felt the direct effects of them in the past.
No matter what stage you’re at in the journey of manufacturing, whether you already have products on the market or an idea on the table - we’re here to help. We support our clients at every step, from pre-production runs to sub-contractual agreements and volume manufacturing.
If you are looking to work with a manufacturer you can trust, talk to us today and you’ll find an expert electronics manufacturer to make every Black Friday a success!
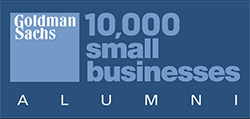
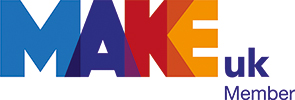