News
Apprentices and the manufacturing skills gap
Published Wednesday 15th May, 2019
In an economic climate of uncertainty and high unemployment, it seems crazy that companies are struggling to find skilled workers, but the growing manufacturing skills gap suggests that it's a big problem.
As graduates move into different sectors, engineering and production suffer, with many posts going unfilled due to candidates' lack of experience or even because there are no applicants at all!
We take a look at how we ended up with this skills gap in manufacturing, and why the electronics industry is recruiting apprentices to ensure a healthy and competitive future.
The skills gap and how it affects the manufacturing industry
A skills gap is the difference between the skills the available workforce has to offer and the skills the employer requires. It's an ongoing issue in manufacturing industries because as the Baby Boomer generation hit retirement age, their breadth of knowledge is being lost with them, and the workers who would naturally replace them often see manufacturing as an unappealing career path.
Many of those potential employees still see manufacturing as a dirty and smelly industry full of low-paid and unskilled jobs, but with the emergence of the fourth industrial revolution (Industry 4.0), there's hope that this attitude can change...
Electronics in Industry 4.0
Industry 4.0 is really a refinement of Industry 3.0 - when computers and manufacturing automation changed the factory floor forever. Rather than reinventing the wheel, the fourth industrial revolution will be an advancement of these systems and includes the Internet of Things, high-performance robotics and 3-D printers.
Improvements in cognitive computing and AI, alongside more powerful design software and manufacturing processes, are making the electronics industry more attractive to potential employees.
Apprentices in electronics
Until fairly recently the expanding manufacturing skills gap wasn't a challenge that the electronics industry had to face, but we've seen this trend hit our sector too over the past few years. Fortunately, there does seem to be an effective answer in the shape of apprenticeships.
With engineering, design and manufacturing jobs in the electronics sector being so highly skilled and multi-faceted, it's becoming more important to invest in in-house training. Even in a sea of potential employees, finding those with the required skill-set is becoming so hard that, in some cases, it's barely cost-effective to search! Instead - and this is true in our own experience - it's better to train them yourself from the ground up.
While most businesses have traditionally looked to university graduates for fresh recruits, there's a definite trend towards hiring apprentices – especially with improved government incentives for small businesses to do so. Providing on the job training alongside education is a time-honoured tradition that helped to create the last manufacturing boom, and there are good signs that it can do the same during Industry 4.0.
With 98% of apprentices happy to recommend their employers to a friend over the last five years, it looks like apprenticeships are here to stay. This has had the knock-on effect of encouraging universities to spread their nets further afield and invite more vocationally-minded students to attend, with the potential to gain a career and a degree.
It's interesting that as we make such huge advances in our technology, the answer to bridging the manufacturing skills gap is to reinstate a system that had such a positive effect in previous generations.
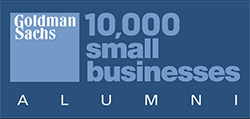
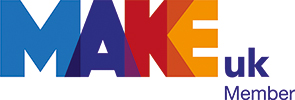