News
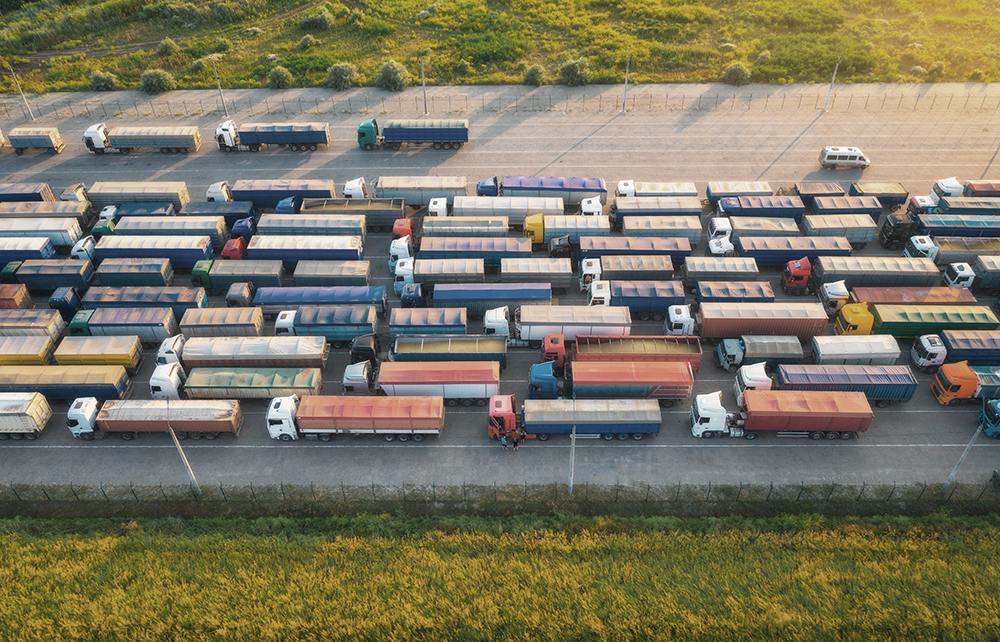
Manufacturing Supply Chain Management Post-Brexit
The impact of Brexit and Covid-19 on manufacturing supply chain management
Unless you’ve been living in an alternate dimension for the past few years, Brexit and the coronavirus pandemic can’t have escaped your attention – and if you operate in electronics or any other area of manufacturing, supply chain management will almost certainly have been your biggest obstacle to overcome in the face of them.
As the two big issues currently impacting manufacturing supply chains, we’re taking a look back at where it all started, how we tried to prepare for Brexit and react to the pandemic, plus share a few strategies that might help other manufacturers to mitigate supply chain management issues.
A look back at Brexit and preparing for our exit
Since the result of the Brexit referendum in June 2016, every manufacturing business in the UK knew it would have some impact on their operations. The looming threat of increased border checks, custom fees and logistical hold-ups led to many trying to predict and mitigate the potential supply chain issues that would follow our exit from the EU.
At Daletech, we took the rapid step of conducting a full audit and risk assessment of our supply chains and investigating strategies to help us mitigate any likely issues that would impact our business, and consequently our clients.
As our official exit on the 31st January 2020 approached, the issues facing our supply chains were already being felt. Post-transition, manufacturers and suppliers entered into a harsh period of adjustment, as the realities started to reveal themselves and trucks by the, well, truckload, queued up at the borders trying to navigate the new systems and processes in place.
How the pandemic presented additional strains on supply chains
Just as suppliers and their manufacturing clients started to find ways to manage their networks and reduce the impacts of the evolving Brexit situation in early 2020, the world was suddenly plunged into a global pandemic, thanks to coronavirus and Covid-19.
Already strained and under pressure, suddenly supply chain management found another complex obstacle to overcome – with whole countries in lockdown, material supplies drying up and international logistics becoming even more fraught and unpredictable. That’s not to mention the Suez Canal blockage in March this year that created yet another logistics and supply chain backlog.
These issues demonstrated just how fragile manufacturing supply chains really are, especially in areas such as electronics where many of the raw materials needed are sourced overseas. This is where transparency and future-proofing comes in – disruptions impact every other area of business, so robust supply chain management, contingency planning and client communication must be the cornerstones of every manufacturer’s business approach.
How supply chain issues have impacted the electronics industry
Facing ever more complex supply chain issues thanks to European and global shifts, it’s time for the manufacturing industry to build resilience for ongoing and future issues.
According to figures from the Office for National Statistics (ONS), imports from the EU fell by over 28% after just one month of our departure – at a total value of £6.6bn. Shipment costs have risen, containers struggled to find their way to their destinations thanks to pandemic disruptions and road logistic costs have increased fourfold in many cases since Brexit was finalised. Without finding ways to keep on top of these issues, manufacturing clients and customers will suffer.
Our own experience of Brexit and the pandemic has not been a pretty one, and by the nature of the issues we’ve encountered, they’ll be universally felt across our industry.
Right now we have a very real problem around a global shortage of electronic components across the board (pardon the pun). The pandemic has probably been the most influencing factor due to manufacturing and sourcing of materials and components slowing down - or stopping entirely in some cases - resulting in shortages that are subsequently causing major problems in production.
As an example, one of the IC manufacturing companies we use, NXP, was recently showing a 52 week lead on some components – yes, a full year. That’s a long time for an OEM to wait to get their product on the road. Previously we were working with lead times that could be as quick as two to three days, with a maximum of around 10 days for specialist items.
When it comes to stock shortages, unfortunately, it’s often that case that we don’t know there’s a problem until the consignment fails to arrive, and we’ve found ourselves spending more time than ever trying to source and procure alternative parts.
Thankfully, because we’ve always focused on transparency and clear communication, we’ve been able to maintain good relationships with our customers. On the flip side, this is genuinely the most significant and difficult situation we’ve seen impact the electronics manufacturing industry for many years – perhaps ever.
To put some of these supply chain problems in context, let’s look at some stats put together by another electronics consultancy, ByteSnap Design, as a result of a survey they conducted in April/May of this year, across multi-industry electronics professionals:
- More than 56% have been affected by the coronavirus pandemic
- 34% have experienced longer lead times for components
- 24% have been unable to procure the parts and products they need
Apart from the impact of availability, there are also costs to consider – scarcity and increased freight and customs costs all lead to inflated prices, usually impossible to absorb at the point of manufacture and therefore having a knock-on effect on end-product prices, both for OEMs and their customers.
We’ve seen significant price increases across the board for all components, something we’ve never experienced prior to the double whammy of Brexit and the pandemic crisis. At the point of quoting on an electronic assembly one particular component was costed at £2.86, but a week later, once we’d received the PO from the customer and processed to purchasing stage, that component had increased to £18.74, and with only 50 items available.
This again is where our transparency comes in: it’s so important to explain supply chain issues to the customer and find a solution to help them deliver their own products.
Managing post-Brexit and covid supply chain issues
According to ByteSnap’s survey, 53% of respondents reported a negative impact on their business as a result of Brexit, with just 3% feeling a benefit. Additionally, 70% of them also reported ordering from/moving to Europe has increased paperwork loads, costs and general difficulties in the supply chain.
For us and our fellow manufacturers, we’re still navigating what are very uncertain times, and are continually talking to our customers about how their world has changed since the pandemic and what additional services we could offer to help them succeed.
It’s been - and remains - interesting to travel along in this sea of change and we’ve had to adapt in order to keep business running and our customers happy.
The main way we’ve been navigating these issues is through the implementation of a digital transformation strategy while also ensuring we’re aware of changes to our customers’ working practices so we can continue to support them.
We’ve shifted our approach to become totally process-driven, which in turn has driven efficiency. There have been and continue to be significant challenges, and we hope that the resilience we’ve demonstrated and our team’s problem-solving skills will help us to maintain our high standards of service to our customers.
We’re constantly taking temperature checks of the manufacturing sector in our region and talk regularly to our suppliers so that we’re aware of any new problems that may be arising.
Future-proofing supply chain management in manufacturing
Ok, it may not be possible to fully future-proof and contingency plan for every possible supply chain scenario, but the above strategies, alongside our policy of continuous improvement, have helped us to keep up with the Covid/Brexit situation to a fairly successful degree.
Despite the issues that surround us, we continue to be committed to ISO 9001:2015 and have just appointed a new auditor to ensure that we’re practising what we preach! We have ambitious growth plans based on sustainability and scalability, and we’re investing in our apprenticeship programme to ensure that we have a pipeline of young bright talent on board – so it’s safe to say that we’re confident in our abilities to keep moving our business and our customers’ products forward in spite of the hurdles that keep cropping up on our path.
As we continue to press forward, we’re fully accepting of ongoing supply chain issues and component shortages that we’ll need to keep navigating – but by upskilling our staff, keeping an eye on the global situation and making the most of our new digital software, we’re facing the future with a positive attitude.
If you’re a manufacturer of electronics or otherwise, we’d be interested to hear the particular problems you’ve faced in your supply chain management due to Brexit and the pandemic, how you’ve managed to overcome them and even how we may be able to help – join the conversation here!
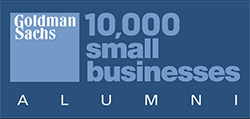
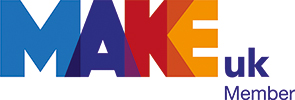