News
How does the PCB assembly process work?
Published Tuesday 24th July, 2018
The printed circuit board (PCB) has such an important but unseen role in the modern world that it’s easy to take it for granted, but understanding the fascinating processes involved in PCB assembly shows how seriously electronic manufacturers take these small but powerful components.
Let's take a look at some of the generic processes used to ensure your electronics give you years of trouble-free service.
PCB assembly all starts with the base
Whether the board is going to be rigid, flexible or metal core, the basic design of the base will be pretty much the same:
- Substrate – the base material that determines the degree of rigidity or flexibility.
- Copper – used as a conductor, copper foil is laid on one side for a single-sided PCB and both sides for a double-sided board.
- Solder mask – the characteristic green colour we associate with PCBs comes from the solder mask, which keeps everything in place and prevents shorts by insulating copper traces from other conductive materials on the board. The solder mask also contains holes, which serve two purposes: to allow components to be soldered to the board and to protect the rest of the board from solder.
- Silkscreen – An essential layer, the silkscreen contains all of the printed information in symbols and characters that indicate each component's function.
PCB to PCBA
Although we often use the term PCB to describe the finished board that’s fitted to your electronic device, it’s actually a PCBA - a printed circuit board assembly - which is, essentially, the PCB plus all of the assembled components.
Every manufacturer will follow their own unique PCB assembly process, depending on their specific needs and preferred testing procedures, but the basics will be largely the same because they've been proven to lead to a successful manufacturing solution.
Some of the most frequently used processes in PCB assembly
With the vast majority of modern boards being manufactured using surface mount technology (SMT) - meaning that components are mounted and soldered onto the surface of the board - we'll concentrate on introducing you to the most basic process used:
- DFM check – the design for manufacturability check (DFM) determines whether there are any design flaws or potential issues before manufacture begins. It can spot errors and potentially streamline and save money by identifying areas where the design could be made more efficient.
- Solder paste – solder paste is applied to the board using either a machine, or manually through a stencil to ensure that the paste is only added where it’s needed.
- Pick and place – traditionally components were placed on the board by hand using tweezers, but this process is now almost always performed by machine to ensure absolute accuracy and greater efficiency. Parts are placed directly to the soldered areas (sometimes with dots of glue if wave soldering is going to be used) in preparation for the soldering process.
- Reflow soldering – the boards are now passed through a reflow oven on a conveyor belt (not unlike a commercial bakery) and heated to temperatures of around 250°C to melt the solder. Instead of cooling quickly and risking damaging the boards, they’re then passed through ovens of gradually reduced temperatures to ensure that cooling is controlled.
- Inspection – various forms of inspection are used, from:
- Manual inspection
- Automated Optical Inspection (AOIs are machines with many cameras that allow large batches of boards to be checked from every angle with speed and accuracy)
- X-ray inspection (used rarely for complex PCBs with many layers)
- Testing – there are many testing processes used, but they all have the same goal: put the PCB through stress testing to determine if the design and completed board is robust, effective, fast and long-lasting.
If you'd like to know more about the exact processes Daletech uses in our PCB assembly, feel free to drop us a line - and we're always happy to meet up over a cup of coffee and talk you through our services if you wish!
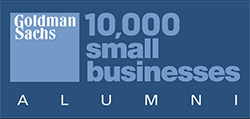
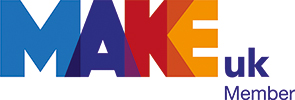